|
 |
 |
|
 |
 |
 |
|
 |
|
Input/Loss Method -
Tube Failure Detection
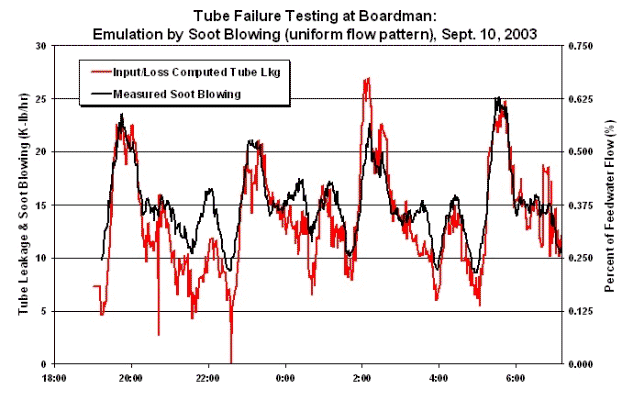
Input/Loss has an ability to rapidly detect tube failures and
their location within the Steam Generator, without direct instrumentation. By
"location" implies the heat exchanger in which a tube has failed, and thus
leaking to the combustion space; e.g., a tube failure in the Economizer,
Reheater, etc. Rapid detection reduces damage, minimizes degraded heat rate, and
minimizes repair time, thus saving million of dollars.
Tube failures are
detected through use of system stoichiometrics, in combination with an ability
to correct effluent data through use of optimization procedures. A Stack H2O
instrument is not required, nor is its presence a panacea. The location of the
failure within a Steam Generator is determined through use of energy balances
and iterative techniques - made possible only because of the integration between
effluents and boiler efficiency. Further, the model also indicates how the stoichiometric mechanism of a tube failure has been identified.
Effluent water concentration (at the Stack) may consist of many sources: water
formed from the combustion of hydrocarbons; free water born by the fuel;
moisture carried by combustion air including air leakage; heat exchanger tube
leaks; water added at the point of combustion (e.g., steam used to atomize
fuel); pollutant control processes resulting in the in-flow of water; and soot
blowing. All such sources of water are addressed by Input/Loss Methods through
system stoichiometrics or direct measurements and integrated through a high
accuracy boiler efficiency ... in combination with an ability to correct COP
parameters through ERR-CALC procedures.
To date, the Tube Failure Model has successfully identified a number of tube
failures at several installations. Indeed, its initial success at Portland
General Electric's Boardman unit has lead to an aggressive testing program
running from September 2003 through March 2004. This effort routed blow-down
lines from the inlet heaters of all major heat exchangers to the combustion
space. The blow-down flows were individually metered. Thus through selected
blow-downs, proof-of-process testing demonstrated the predictability of the Tube
Failure Model. In addition to this direct injection, testing involves emulating
tube leakage using soot blowing steam: by simply declaring soot blowing flow to
be an unknown and allowing the Engine to compute a "tube leakage", then
comparing results.
Results from the Boardman testing are spectacular, meeting all original
objectives:
-Detection sensitivity is demonstrated at the ±2,000 lbm/hr level
(0.05% of feedwater flow).
-Leak locations were successfully predicted in all five heat exchangers
tested.
-The thermal impact of tube leakage is a function of leakage location;
as
demonstrated by test, and assuming a 40,000 lbm/hr leakage,
effects include: 1.0% ΔηB in boiler efficiency at the Economizer,
varying to 0.5% at the Reheater. Before this testing such losses
were unknown to the industry ... as tube leakage was under-
appreciated.
Comparisons to soot blowing flow are presented above as are the results from a
direct injection. Bear in mind that a 2,000 lb/hr resolved tube leak is only
0.05% of feedwater flow at Boardman, this is well within typical data chatter
associated with feedwater flow metering. However, Input/Loss system
stoichiometrics are sufficiently sensitive to allow for such detection even at
these low levels.
View Video
on the "Detection of Tube Leaks and Their Location Using the Input/Loss
Methods" ->
Read technical paper on the "Detection of Tube Leaks and Their Location
Using Input/Loss Methods" ->
|
 |
|
|
Privacy | Contact Us
© 2011 All Rights Reserved. Exergetic Systems, Inc. |
|
|
|